Welcome to our inaugural #MechanicMonday, where we shine a spotlight on our team’s exceptional skills and dedication to excellence. In this edition, we delve into a compelling case study involving Morin’s swift action to address a critical issue for a southeast power plant, showcasing our prowess in industrial pump repair and emergency pump refurbishment.
The Challenge: A Critical Setback at a Southeast Power Company
This power plant encountered a significant hurdle when one of their primary circulating water pumps failed, posing a risk of substantial downtime. With a spare pump available, but the installation fraught with complexities due to the application’s critical nature, the power plant enlisted Morin’s expertise for a swift and effective solution.
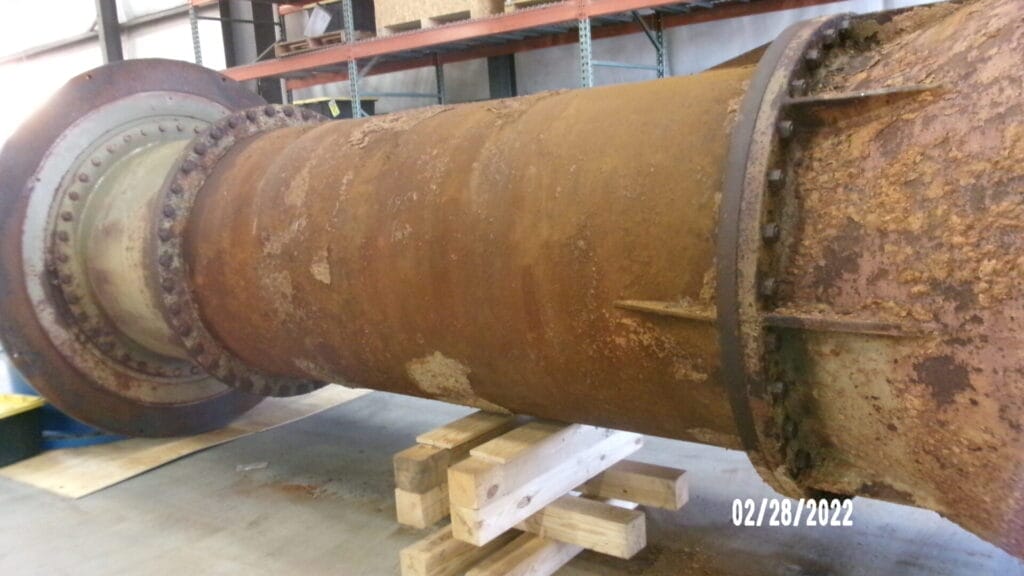
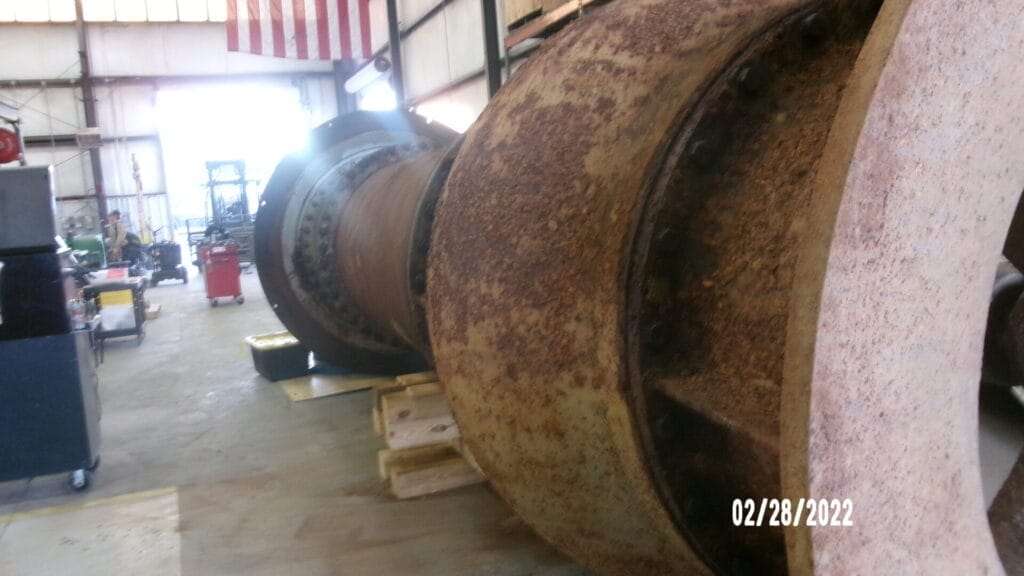
Our Solution: Precision Meets Power
Our journey to resolve this challenge was marked by meticulous planning and execution, outlined in the following steps:
Step 1: Thorough Disassembly and Inspection
Our first course of action involved the careful disassembly of the Sulzer Circulating Water Pump. We conducted detailed inspections, taking precise tolerance measurements and compiling an extensive report with digital imagery and repair recommendations.
Step 2: Precision Restoration
Our restoration process included:
- Installing new marine-grade bronze bearings with exacting industrial tolerances.
- Crafting a new shaft sleeve through precise machining.
- Assessing the impeller and bowl wear rings for reuse, followed by a meticulous refurbishment of the impellers, ensuring a final 2-plane balance to 4WN specifications or better.
Step 3: Expert Coating and Assembly
We applied a durable coal tar epoxy coating to the stationary parts and a marine-grade epoxy for the finish. The assembly was carried out with utmost precision, ensuring every part and material was perfectly aligned and installed.
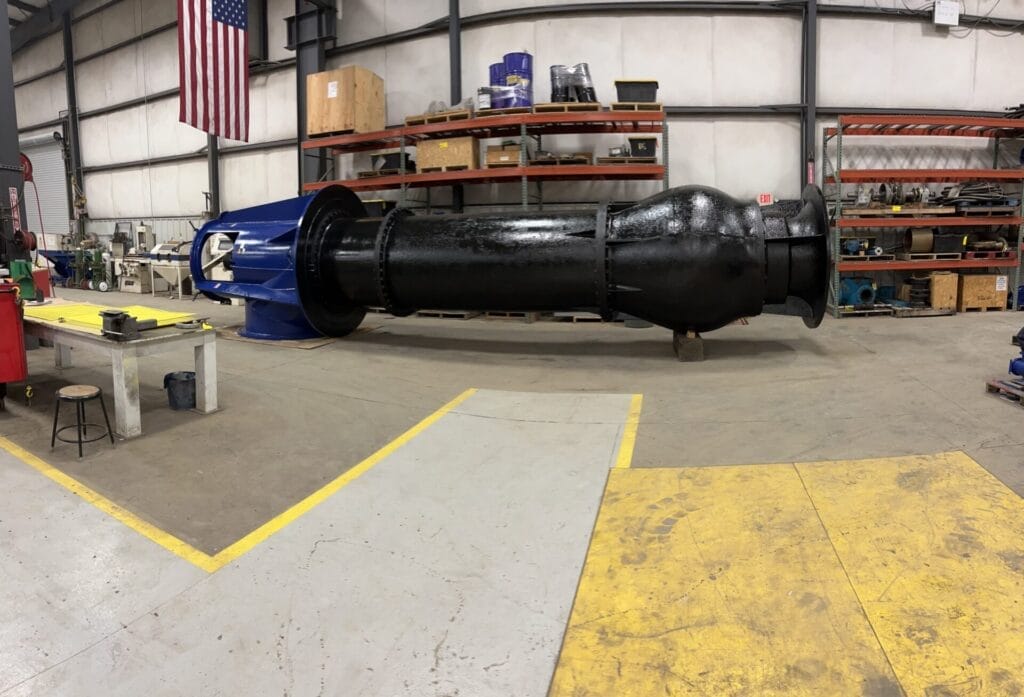

Step 4: Comprehensive Documentation
Our commitment to transparency and excellence was evident in our thorough documentation, from start to finish, including photographic records, strip reports, assembly notes, and balance reports.
Technical Challenges and Expert Insights
Tackling a unit over 30ft long and weighing 35,000 lbs. came with its unique set of challenges. Yet, our team’s expertise shone through. Senior Precision Pump Technician Charlie Bass emphasized the importance of precision, stating, “We use precision, not persuasion. Speed is irrelevant if it’s not done right.” Jodie Murphy, our Lead Precision Pump Technician, added, “To fix the issue we ran into, we needed to make modifications to the existing expansion joint to account for an offset bolt pattern. We also then needed to address the metal rings used to secure these connections. We were prepared for this and had all the right tools and expertise to get this done in the field and complete a reliable connection. Just another day for us!”
On-Site Triumph
Our dedicated team ensured the seamless removal and installation of the refurbished pump and motor, conducting thorough test runs. Working in two three-man teams around the clock, we completed the project in just 10 days, ensuring an uninterrupted power supply to the region.


Conclusion: Beyond a Repair
This project was more than just a repair; it was a testament to Morin’s commitment to delivering exceptional solutions. Our ongoing partnership with this power plant continues to grow, paving the way for future collaborations and success stories.
We extend our heartfelt thanks to our incredible team for making this #MechanicMonday a resounding success!